Is Excel the Best for Construction Site Resource Management?
Is Excel the Best for Construction Site Resource Management?
Introduction
As usual in our articles, we focus on the asset management area in the industry. What we call - asset management, Enterprise Asset Management, billing, delivery, and construction site warehouses is always the same. A fully calculable and accountable way to communicate how much of something is on-site, whether it has been built up, whether it's arrived from suppliers and where (heck) it's lying on site, and whether it needs to be returned to the supplier as we pay for each day's lease.
What Is Excel Used For?
Whether it is a construction site or a manufacturing plant, in each of these places - we won't reinvent the wheel - a spreadsheet is on the crest of the wave. Microsoft(R) Excel(TM) or something else (rarely), practically in every such place there appears such a tool, hundreds of columns, often hundreds of such files counting or showing something. That is because frequently, the employees in the plant have to manage the maintenance tasks assigned to them. ERP systems focus on accounting data, finances - including hard cash - and all resource management elements are just an extension of the main business goal. This results in excellent work concerning the financial management but is not very helpful to the front-line employees fighting to be in complete control. Therefore, a spreadsheet works as a database, something like a converter and calculator.
Why Excel?
If we look at the activities of manufacturing plants, very often companies have their own ERP system. It allows you to efficiently control the financial aspects of the company. It can also have additional modules responsible for maintenance management - but usually, it looks like maintenance in this system is to provide data to the financial part. As a result, the functions are focused on the finances (settlements, reports, costs) and not on the operational aspect of the maintenance teams. Additionally, as we have seen many times, these modules and access to them are limited - usually because of the cost aspect - not to mention flawed mobile and offline access. The management is in charge of the modules, which leaves data input and updates on their shoulders. What is the outcome? Managers get information from employees in the form of documents, printouts, forms, or the well-known Excel sheets and deal with entering this data into the ERP system.
Nevertheless, anyone who has used this type of tool in more significant applications where the data changes significantly, many people work on the data, knows that often the work can look like this: at first, it is fun, then it starts to get tough, the formulas get out, the employee who was supposed to enter something, accidentally damages other data, and finally after half a year of using the spreadsheet on a shared drive "something" happens and the file ends up destroyed. We have copies of the file to do this (because of how often something breaks), and we end up working on 15 versions scattered over users' drives.
Can this be implemented differently? Does it always have to be a conversation about expanding an ERP system or implementing an EAM system from a very, very well-known vendor with an implementation that takes several years?

Alternative
Can It Be Done Differently, and Why AMAGE?
Usually, in fact always, during AMAGE implementations, we encounter worksheets that we import into the system. That is how we transfer the plant's "knowledge" from stored sheets. Sometimes no longer used, but containing an important catalog or historical information. We remove those sheets in favor of a solution that replaces them and provides several functions facilitating their management. Commonly, the spreadsheets' management and updates are done by one person. Someone (area coordinator, UR manager) responsible not only for creating structures and data but also for periodic (daily, weekly) updates from multiple sources and different people. During an era of increasing digitalization and awareness of nearly every employee concerning daily used technology (phones, tablets), such an approach is - to say the least - inefficient.
Strengths of the New Solution - Organizational, Financial, and Technical
The AMAGE system places great emphasis on the distribution of data input. It is no longer just the manager/coordinator but the entire operational plant personnel to provide the data. That allows for quicker updates, distribution, and usage. It also allows for easier coordination of work and visualization of possible problems. Integration with other systems (ERP, DCS, domain systems, e.g., weighing systems, chemical measurements) significantly improves the work.

In this way, the AMAGE system disperses the creation and analysis of information. The main area coordinators
get only information about relevant occurrences and allow them to control the process, despite their form - visualizations, reports, or decision messages. Everything is available on a phone/tablet, making the work and coordination much more efficient. Importantly, our system also integrates suppliers into the entire process on-site. That eliminates the additional need to send, coordinate and check all activities on the construction site and the surrounding area. Significant time savings and avoidance of costly mistakes. All this on a single platform.
By enabling work in the system by the usage of phones, tablets, Internet kiosks, but also devices working in offline mode (without access to the network) such as mobile terminals (handheld) and rugged tablets of various sizes, we increase access to information and the source of their formation. In this case, the basic sheet barrier disappears - only one person edits and enters data after returning to the office. Here we work on the fly and continuously enter and use data.
One of the many advantages of the AMAGE system and this approach is also the ability to involve people from outside the organization. The process of annual reviews, inspection works, and repairs can be delegated to the external subcontractors who also enter data during work. That, with the current trend of distancing employees from third parties, also facilitates such work organization. All of that in a coherent system that not only does away with the mass of Excel sheets in the plant but also gives power to the employees.
Advantages:
- Just like Excel but better
.
- No problems of data corruption, multi-user access, wrong data entry.
- Data is entered by many users - even those who have not entered data into the system before.
- Full history and access to data in every place.
- Definable mechanisms of information flow. Many functional modules operate on the data (service events, rounds, control works, inspections).
Solution Demonstration, Implementation, and Purchase
Contact US
If the described story applies to you at least a little, we suggest that you take a look at our solutions, arrange a meeting, and we will try to find a solution that allows you to regain control of your on-site resources while saving yourself a few gray hairs each month of work. Feel free to contact us.
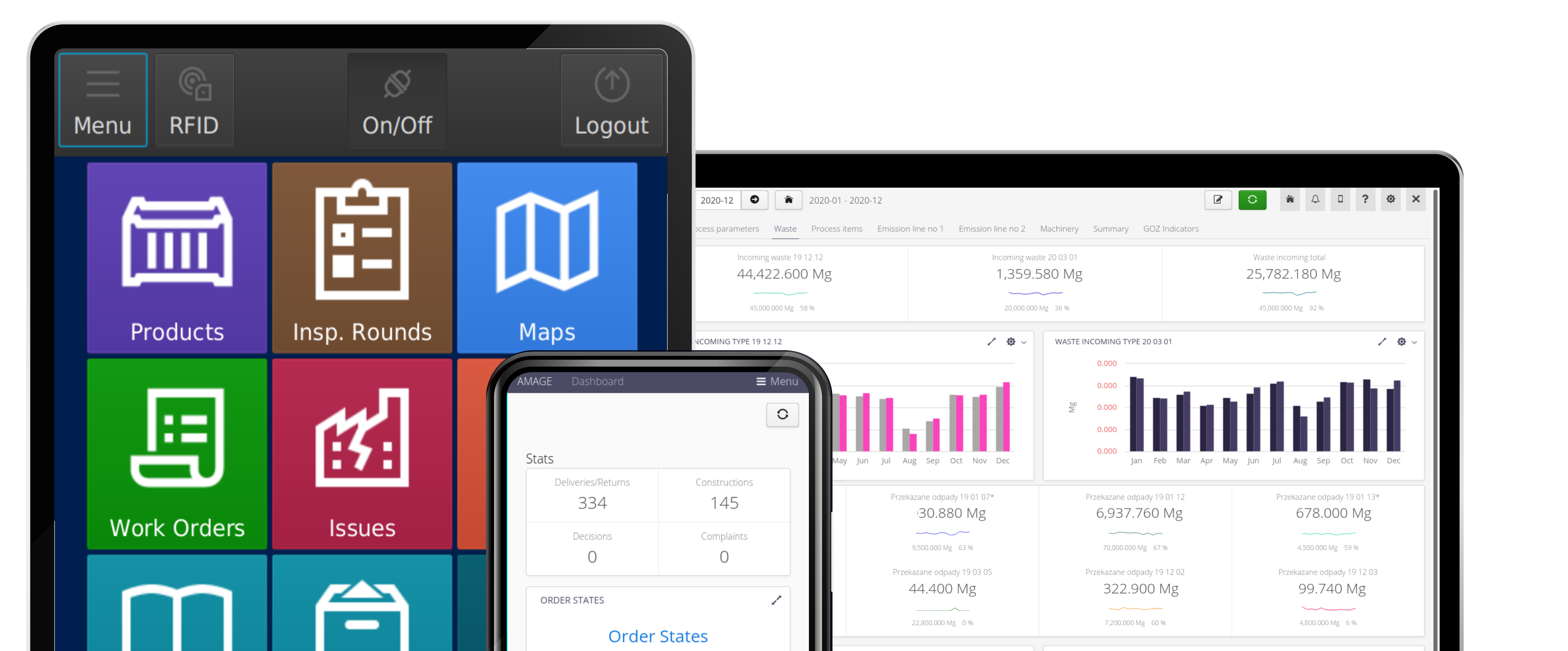