IT Systems for the Industry – General Description
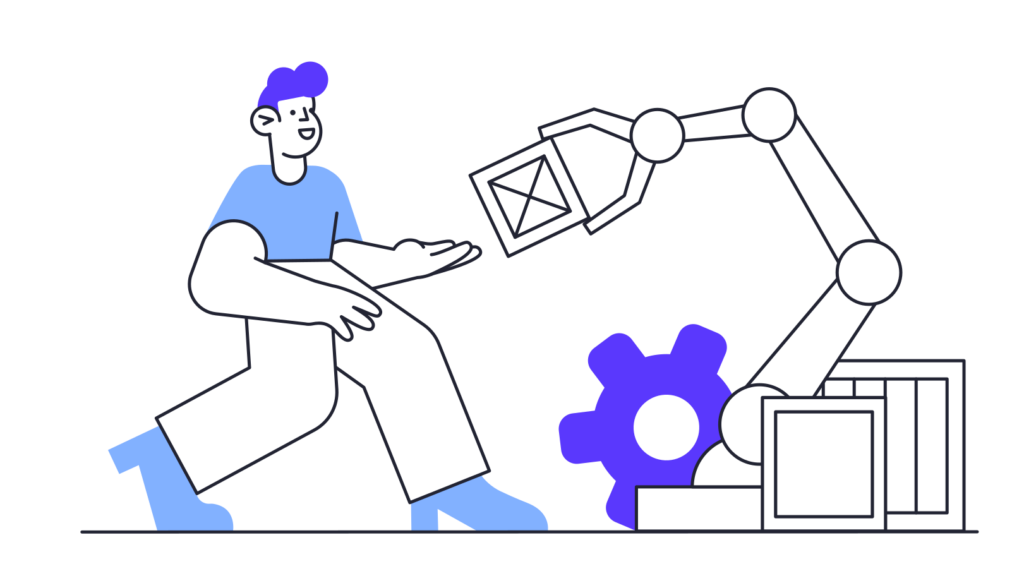
Solutions
IT Systems for the Industry – General Description of the Solutions
AMAGE Systems provides a set of IT solutions that can be applied to a range of industrial enterprises. In particular, plants with continuous production can find modules or feature sets in our solutions that will suit their needs and business profile.
Functionality areas for this solution branch are divided into three blocks: Data Access, Plant Operations, Planning, and Controlling. The modules and functions of the system are shown in the figure below.
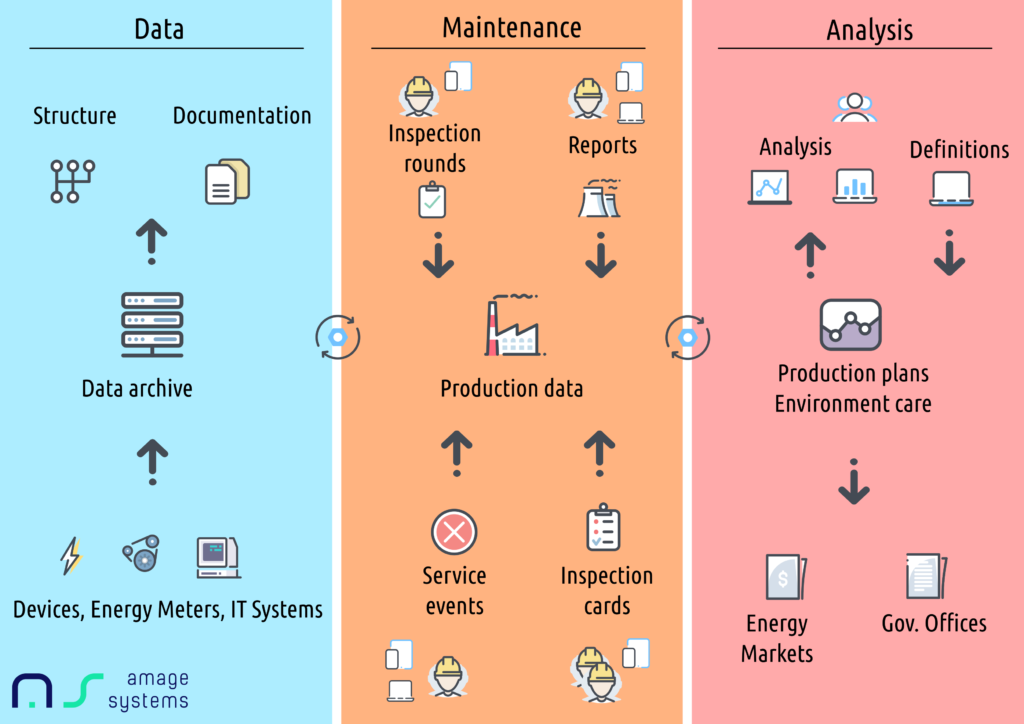
These areas can be characterized as follows:
- Data Area – allows collecting structured data in the system and its presentation. AMAGE can gather data directly from devices located in the plant through its own IIoT devices and data aggregators. It can also integrate with external IT systems through definable modules and import data from structures like XML/XLS/CSV. All this is to build a data archive. This data can be linked to the enterprise resource structure and made available via mobile devices/desktop systems to the users. The data also serves as information for further functional areas.
- Operations Area (Maintenance) – supports the day-to-day operations of the production and maintenance teams at the plant. Functions related to the service events, inspections/control works, and rounds allow efficient organization of maintenance employees’ tasks. The system enables the automation of work and employee notifications. All this data is recorded in the context of the equipment collected in the previous area. In addition, mechanisms related to the supervision of production data, parameters, and production execution have been prepared for production teams. The definition of production parameters, their planned consumption, and technological or contract-related limits allow for ongoing reporting and analysis of the work of the plant operation.
- Planning Area (Analysis) – allows operational supervision of plant operations. Through the definition of production and financial plans (controlling), the system enables monitoring of the plant’s performance and execution of work in the context of actual material consumption and realization of financial plans. Monitoring integrated permit parameters and legal and organizational conditions simplify the work of the environmental inspectors. Integration with external organizations facilitates reporting and financial analysis of the enterprise.
All these areas are characterized by a set of functions and modules that implement defined objectives. We encourage you to read the solutions page for each area and functionality in the solutions section.
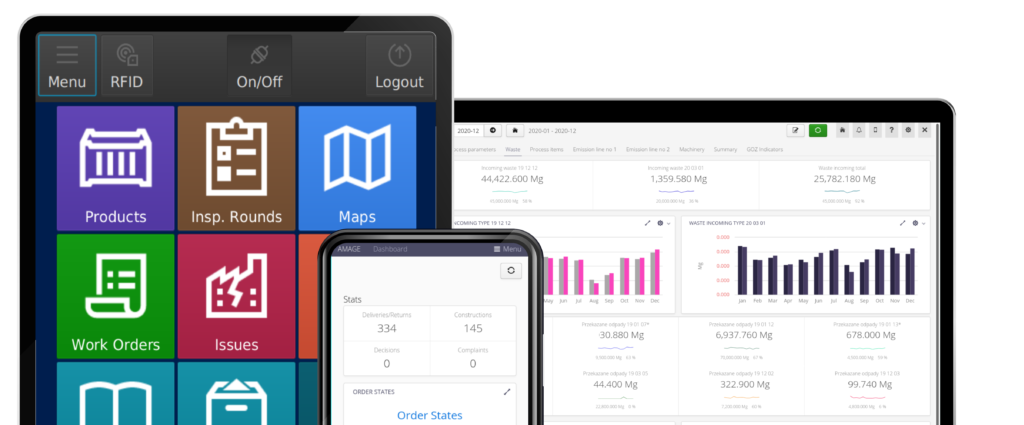