Meet the System – Solutions from the area of orders, deliveries, and supervision of the transportation process
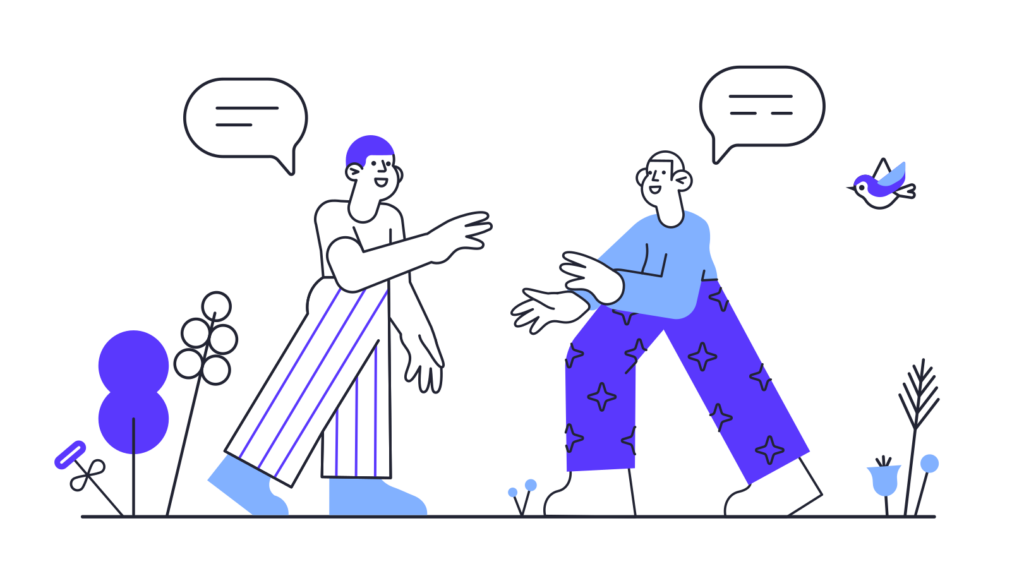
Construction Area
Solutions from the area of orders, deliveries, and supervision of the transportation process
Description
Modules responsible for orders and deliveries allow the realization of the full cycle of handling transports arriving at and departing from the construction site. The system has the ability to define an assortment log (types of items) with detailed information about the transport and financial definitions.
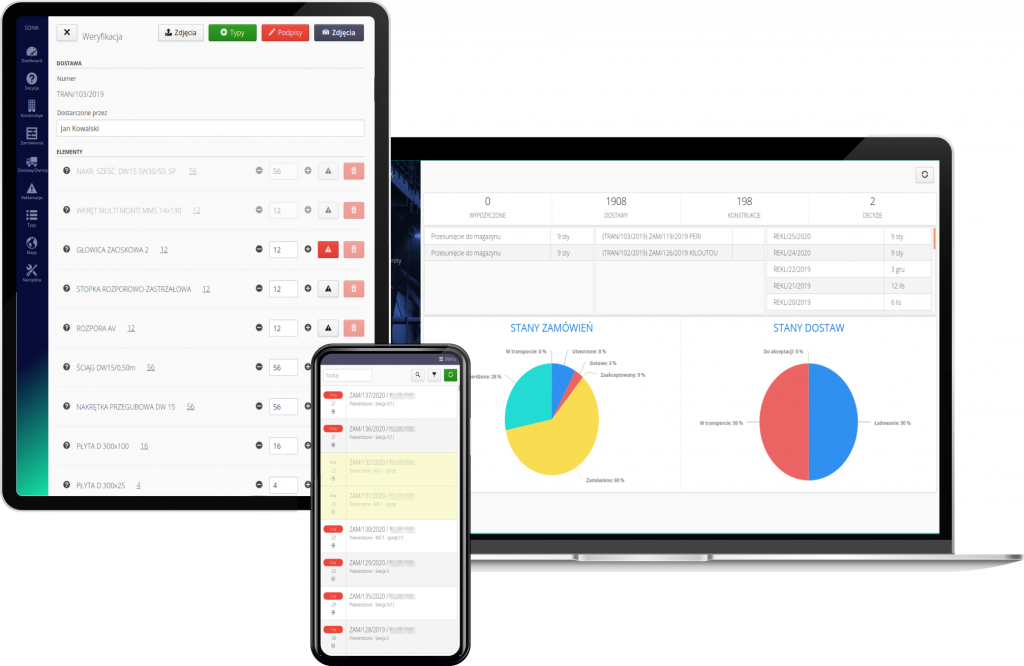
Orders, deliveries, and returns (e.g., for leased items) allow you to ensure full control over what happens to the items and where they are. The user can create orders directly from dictionary data. He can also import a list of items for orders from external CSV/Xls files. It can also form orders based on material plans associated with the project – whether in the context of tasks (work orders) or the technical structure of the project (resource structure). From each of these places, the system will generate orders. It can also automatically send such an order to the selected supplier.
Supplier portals or electronic integrations such as EDI (electronic document interchange) allow automating the transfer of orders but also receiving information about deliveries and transports in progress. That allows further automation of data exchange between all participants, even those (suppliers) who do not have extensive IT systems. The supplier portal facilitates and accelerates communication with the construction site. Full electronic EDI exchange automates communication, ensuring full control of system operation for the area coordinator.
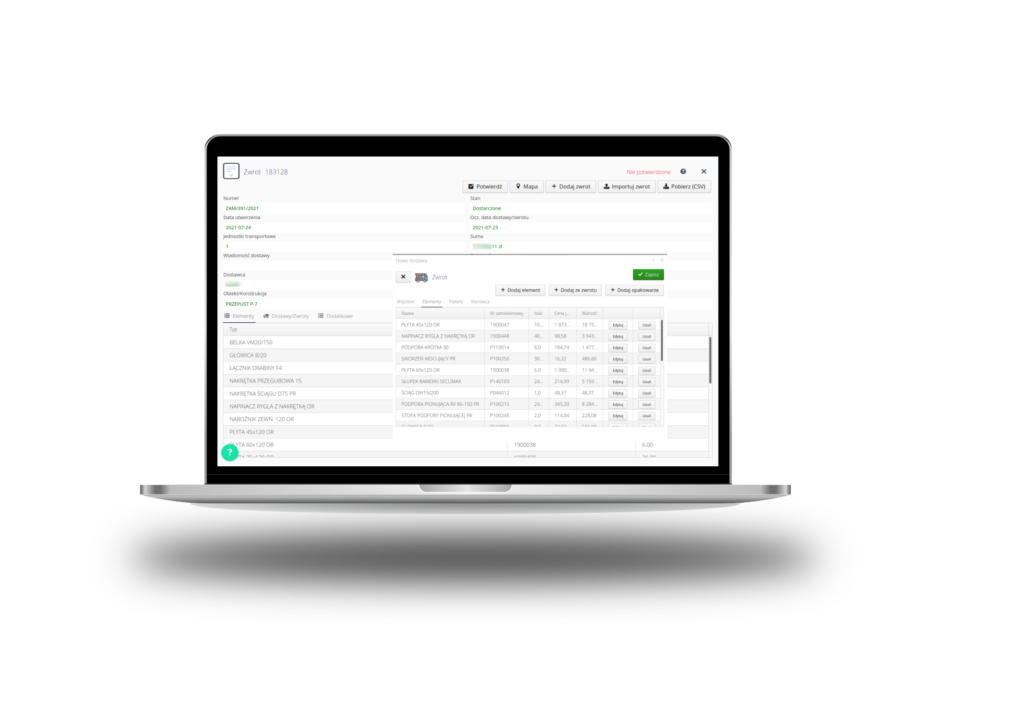
Deliveries appear on-site from many sources, from the supplier portal, overarching ERP systems, or even self-declared in the system. Each such delivery undergoes full loading operations, site inspection, and claim procedures. In each case, we support line workers at the construction site through an interface on a phone/tablet or mobile terminal indicating detailed information on the transport being carried out. When the supplier is an in-house manufacturing plant (enterprises), data can be entered directly into the system during loading by plant employees. In this case, we get additional information about the actual materials in transport.
Checking deliveries allow you to enter information about the delivered goods, modify the delivery declaration and enter information about possible quantity/quality inaccuracies. This data is transferred to the supplier in the form of a complaint. We then enable full electronic circulation of this complaint in the system through the Supplier Portal. During delivery, we ensure traceability of delivery, receiving, and verification personnel. Electronic signatures, scans of badges in the form of cards, and photo documentation fully complete the transport data. Completion of the procedure allows the information to be entered into construction warehouses and further internal distribution.
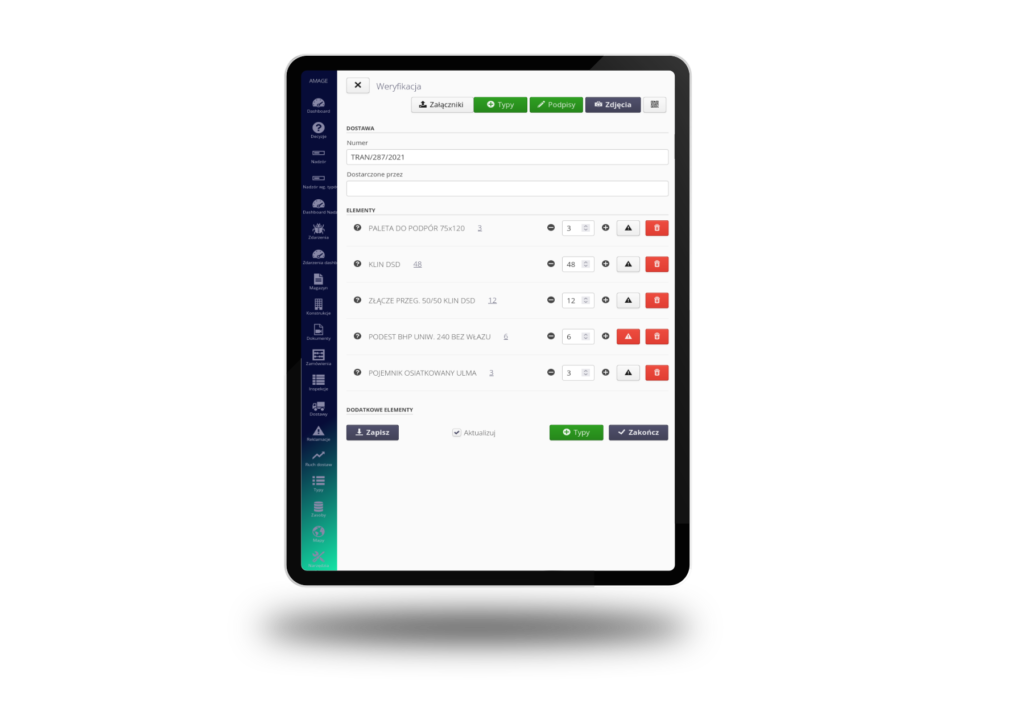
The modules also support the reverse situation, i.e., the procedure for returning materials from the construction site. In the case of leased items, the system supports returning materials from the site, loading them, notifying the supplier of the requirement to deliver transport units, and then loading them onto vehicles. We also support checking the material manually and through direct integration with the supplier’s warehouse systems.
When detailed tracking of the transportation, delivery, and the returns process is required, the system has extensive modules to track transportation (vehicles) and manage delivery queues. With the help of the system, we make it possible to report data in detail and direct vehicles to unloading yards or waiting areas. Based on this information, we receive complete information on completed transports. That allows us to generate information such as concreting logs with detailed information on the times of individual operations.
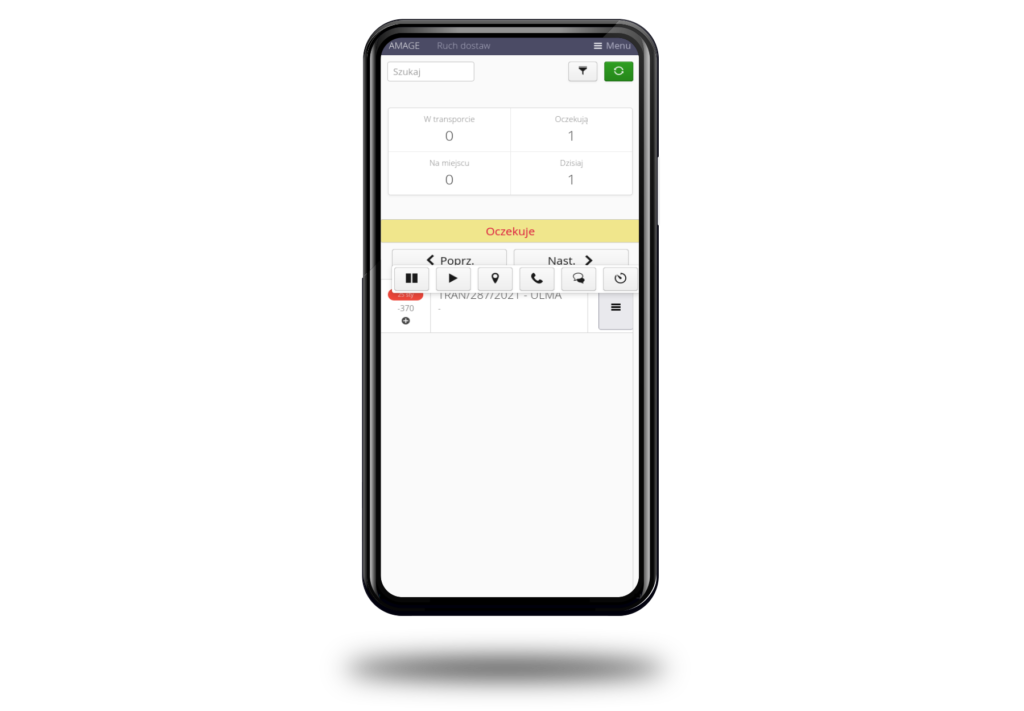
Advantages For the Coordinator
- Integration of order/supply process with material plans, and project requirements.
- Full control over completed orders, deliveries, and returns.
- Documentation of acceptance of deliveries, loading of returns.
- Handling of complaints at every stage of the process.
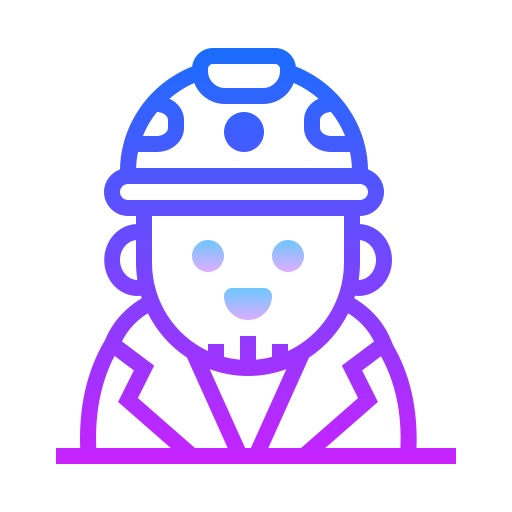
Advantages For the Contractor
- Mobile access to site operations.
- Photo documentation of deliveries, full ability to modify data during checks.
- Ability to perform loading, checks, and claims directly at the point of receipt of goods.
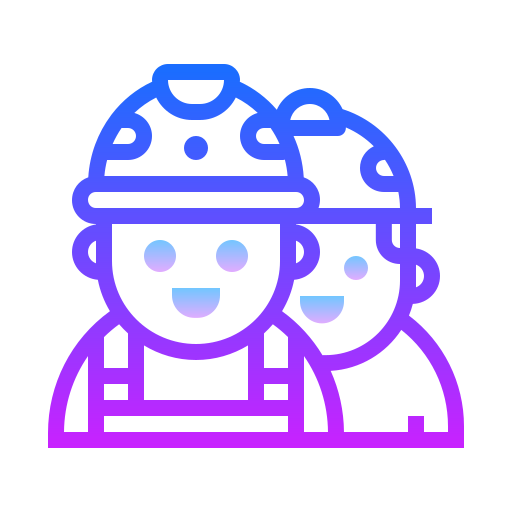
Investment Value and Savings
- By fully controlling the ordering and delivery process, we detect potential supply problems (incompleteness, incorrect material, damage) earlier. We significantly reduce the cost and timing of unplanned deliveries and replenishment.
- Comparison of orders and deliveries with the material plan enables faster execution of work fronts, and coordination of assembly work speeds up projects’ execution.
- Full control over the process of returns allows clear estimation of material on-site, the responsibility of subcontractors, and facilitated completion of material for return. That accelerates the implementation of the investment, reduces the time of leased material on-site, and reduces the cost of leases.
- Implementing suppliers in an electronic information flow (whether through EDI or Supplier Portals) reduces the time/cost of acquiring information on order progress and delivery times and accelerates communication.
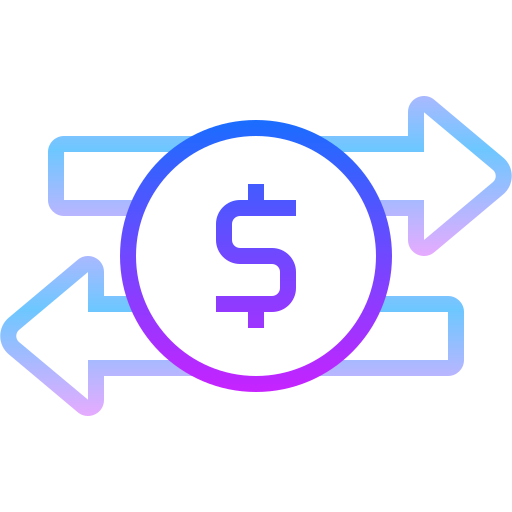
Users
- Delivery area coordinator – manages information, creates orders, and verifies delivery, has full control over process and analytics.
- Site line worker/subcontractor – confirms loading, verifies material shipments, creates formal/photo documentation of the executed process
- Supplier – through the Supplier Portal, handles orders and declares deliveries. Handles claims directly in the system.
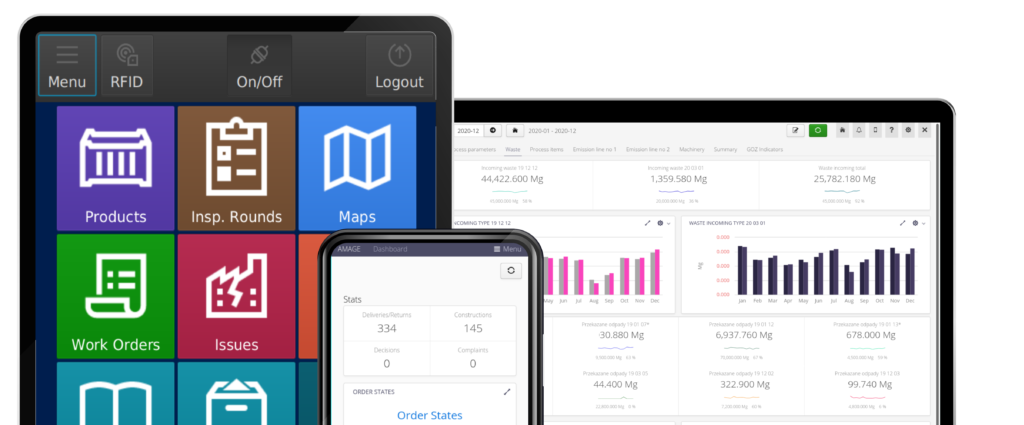
Components
- AMAGE Web
- Supplier Portal